Leveraging Automation to Improve Inspection Quality—An Orthopedic Innovators Q&A
Automation not only addresses labor shortage concerns, but also enhances the overall output by improving the inspection process.
by Sean Fenske, ODT Editor-in-Chief | October 12, 2023
Nick Loxtercamp, Engineering Manager, Orthopedics and Luke Bastiansen, Quality Manager, Orthopedics for rms Company were featured in Orthopedic Design & Technology magazine.
Automated solutions seem to have been slower within the medical device space than other industries. The use of human labor to help ensure quality has been in place for some time. However, automated solutions have continued to improve and have achieved a level that can exceed the capabilities of human labor. As such, having an automated inspection solution for medical device manufacturing may be preferable.
While human workers can be highly skilled in the task for which they are trained, there are downsides that cannot be overcome. Aspects like human bias and fatigue are simply unable to be filtered out from a human worker. On the other hand, an automated inspection solution does not suffer from these weaknesses.
To help provide further insights on the benefits of automated inspection for medical device manufacturing, Luke Bastiansen, Quality Manager—Orthopedics, and Nick Loxtercamp, Engineering Manager—Orthopedics, at rms, a Cretex Medical company responded to a number of questions in the following Q&A. They explain in greater detail the advantages of having an automated inspection system.
Sean Fenske: When it comes to inspection, why can the “human element” be problematic?
Luke Bastiansen: One thing I’ve learned from my time in quality and manufacturing is 100% manual inspection is never truly 100% effective. There are many reasons for this, but the primary causes I consider problematic are subjectivity of the criteria, attention span or fatigue of the inspector, and, perhaps most common, simple human error. Let’s face it, regardless of the task and no matter how much skill or training someone has, we as humans are prone to making errors, whether it’s due to distractions, lapses in concentration, or simply just an oversight. Unfortunately, these innocent errors can have very serious downstream consequences in the medical device industry and may even compromise patient safety.
Fenske: What advantages does automation bring that help to improve quality?
Bastiansen: Many of the issues related to human error in inspection can be solved or mitigated by utilizing automation. For example, several pieces of equipment we have implemented at rms Company have drastically decreased the potential for human error, as this equipment does not experience lapses in concentration, encounter distraction or fatigue, and is free from personal bias and subjectivity.
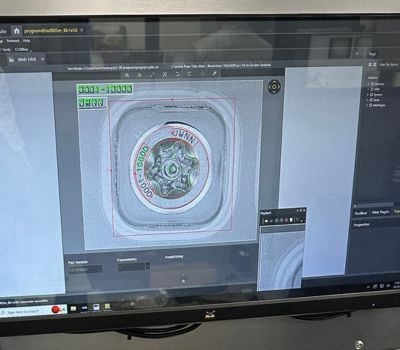
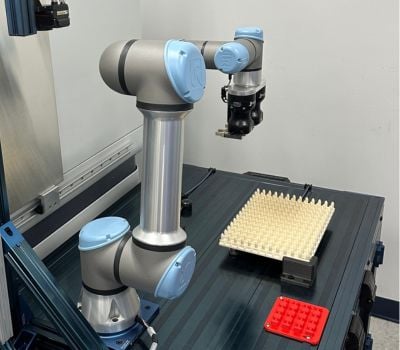
- Safety: Adding automation can improve the health and safety of workers by removing them from situations that could pose potential risk.
- Increased Efficiency: Automation significantly reduces inspection time compared to manual methods. No fatigue and the systems can work around the clock, which leads to quicker results and increased throughput.
- Data Collection and Analysis: Automation enables the collection of large volumes of data during inspections. The data can then be used for trend analysis and process optimization. Which helps provide valuable insight for continuous improvement.
- Faster Reporting: Automated inspection systems generate inspection reports quickly. This would allow for rapid decision making and faster corrective actions, if needed.
- Remote Monitoring: Several automated inspection systems can be monitored and controlled remotely. This allows real-time data to be monitored from any location.
- 24/7 Operation: Automated systems can operate continuously, allowing for inspections to be performed during non-working hours. This maximizes the utilization of equipment and facilities.
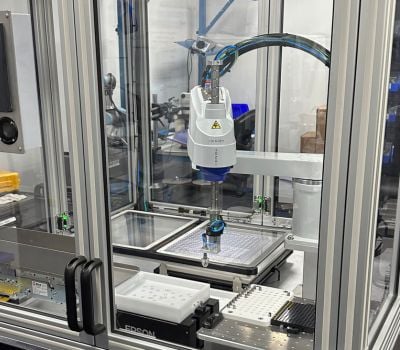
Our dedication to safety, employee growth, and staying at the forefront of innovation guarantees automation will remain a pivotal element of our competitive edge, serving as an integral component of our strategy for continuous improvement and our commitment to harness all its benefits.