How Industrial CT Scanning Improves Additive Manufacturing
OEMs are seeking manufacturing partners who can leverage multiple technologies to design and fabricate the instruments for orthopedic procedures.
by rms Company | September 7, 2022
Cretex Medical | rms was featured in BONEZONE magazine.
When most people hear the phrase “CT scanning,” an image of a gowned patient being pushed into a giant chamber comes to mind. This type of CT scanning is a powerful diagnostic tool in the medical field, and it can also assist in designing additively manufactured parts in the medical device industry. Just as medical professionals read patients’ CT scans to diagnose conditions, device designers can use patient data to recreate their anatomy and manufacture models, guides and even patient-matched implants.
Industrial CT scanning follows the same process, the difference being parts and products are scanned instead of patients. In the coming years, industrial CT scanning will play an increasingly key role in facilitating the use of additive manufacturing (AM) in the medical device industry. With recent breakthrough improvements over the last several years, CT scanning is proving to be more cost-effective, detailed and faster than conventional measuring methods.
Reduce Costs
Industrial CT scanning is not a new technology. People have been CT scanning parts for decades, but it is still underutilized. Historically, CT scanning metal objects was an expensive, time-consuming process. Those labels are quickly disappearing thanks to technological breakthroughs over the last 15 years. High-powered systems, along with automation, cloud computing, and software developments have drastically lowered the cost and time necessary to obtain and evaluate high-resolution, quality CT data. In many cases, CT scanning is now more cost-effective than traditional evaluation methods like coordinate measuring machines (CMM).
Perform Non-destructive, Detailed Evaluations
Today, nearly all AM applications for end-use devices leverage the manufacturing flexibility of additive to broaden the design window of the product. It is vital that manufacturers ensure organic, complex AM products are geometrically accurate for patient safety; however, these geometries are, by nature, difficult to measure with methods like CMM and gauging. Industrial CT scanning, paired with CAD comparison software, is an ideal tool for verifying difficult-to-measure geometries.
CT scanning can provide a more detailed evaluation of porous structures than traditional methods.
Nearly every medical product produced via additive manufacturing has some degree of surface modification, lattice, or porous structure integrated into the part design. Currently, the standard practice for measuring these types of structures is a time-consuming and destructive metallography technique. This technique is not only cost- prohibitive to conduct on a regular basis, but it also provides only a snapshot of the entire structure corresponding to a single plane. Industrial CT scanning is one of many evaluation techniques referred to as non-destructive testing. This means it can provide information about the integrity and quality of a part without destroying the part in the process. Instead of only getting a snapshot of a complex structure via metallography, CT scanning provides information on the entire part allowing for a much more thorough evaluation.
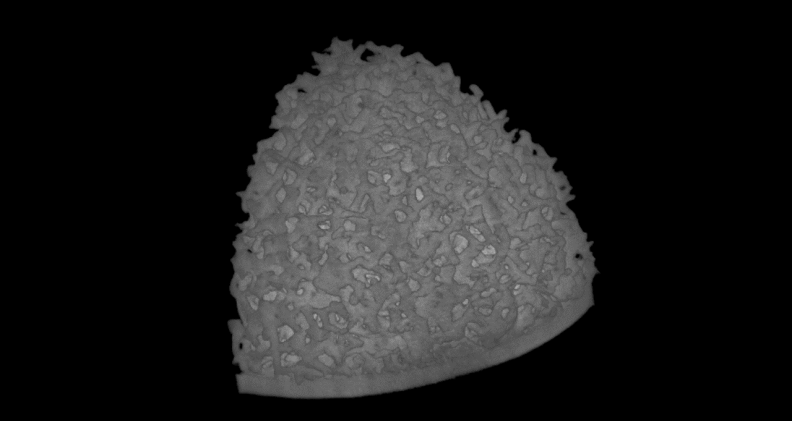
Save Time
In fracture-critical applications, it is crucial that the component has no critical defects. One way the AM industry has safeguarded against the presence of defects is by subjecting AM metal products to a hot isostatic pressing (HIP) heat treatment following the AM process. The combination of heat, time and pressure acts to close and eliminate any internal porosity in a component. However, HIP is a relatively expensive and time-consuming process. Adding HIP to the process flow for an AM product typically adds at least two weeks to the production cycle. For products like patient-matched implants, an additional two weeks can be quite problematic, as there is a patient who is typically in pain and immobile waiting for their custom implant to be manufactured.
It is possible to evaluate AM metal products for the presence of manufacturing defects such as cracking, lack of fusion, and porosity with CT scanning. By leveraging industrial CT scanning, manufacturers can ensure there are no critical defects in their products and eliminate HIP from the workflow, gaining several crucial days in delivering implants to patients.
Process Development, Validation and Monitoring
Additive manufacturing processes can be complicated with many processing variables that need to be dialed-in to produce high- quality products. These processing variables can alter the surface roughness, microstructure and dimensional accuracy of the components you are producing. They also have the potential to introduce defects such as keyhole porosity, lack of fusion, cracks and inclusions into the material you are producing. The foundation of a set of robust processing parameters is their ability to make solid, dense material that is free of critical defects.
Historically, process engineers have relied on tools like Archimedes density measurements, metallography and mechanical testing when developing AM processes to determine whether they were producing quality material. CT Scanning provides a superior and more efficient means of garnering the same information. By combining CT scanning with the ability to produce a single build plate of AM parts containing a matrix of processing parameters, process engineers can develop AM process parameters in a matter of days.
Schematic demonstrating a design of experiments utilized to identify optimal processing PBF-L processing parameters utilizing CT scanning (courtesy of Zeiss Industrial Quality Solutions)
One of the challenges of using AM to produce medical components is the requirement to validate the process to show objective evidence that the process outputs are predictable and meet a certain level of statistical capability. CT scanning is also being leveraged as an evaluation tool to facilitate faster process validations and avoid more expensive and time-consuming destructive testing. In fact, CT scanning has become so cost-effective that process outputs that were previously validated because verification was seen as too burdensome can now be measured in a production environment.
Conclusion
These are a few examples of how industrial CT scanning compliments additive manufacturing. There are many others, including root-cause analysis, surface roughness evaluation, and first-article inspection.
rms Company believes that leveraging industrial CT scanning will allow us to continue to improve and grow the capabilities of our AM division. rms Company has established a partnership with the industrial CT scanning experts at Lumafield and Zeiss to provide this service to our customers.
Please reach out to us to learn more about how we can leverage industrial CT scanning to develop and produce your products.
The Power of Cretex Medical
rms Company provides contract manufacturing of high-quality, tight-tolerance medical implants, components and sub-assemblies using innovative technology, including additive manufacturing.
Collaboration across the Cretex Medical family of businesses ensures a simplified manufacturing process for our customers’ medical devices. Our expertise in multiple areas, including precision machining, surgical instrumentation and sterilization cases and trays, provides a single point of contact. Each Cretex Medical company has specialized capabilities allowing us to support customers’ projects from prototype through finished sterile-packed device.